鈦合金棒材通常帶有較高的加強(qiáng)筋結(jié)構(gòu),零件形狀復(fù)雜且尺寸較大,對棒材制作精度要求高等導(dǎo)致鈦合金棒材加工困難。傳統(tǒng)的鈦合金棒材講過方法以鍛造成簡單形狀的毛坯為主,再結(jié)合現(xiàn)代化數(shù)控加工等方法逐個(gè)加工,提高的加工成本,所獲產(chǎn)品質(zhì)量強(qiáng)度也明顯降低[1]。
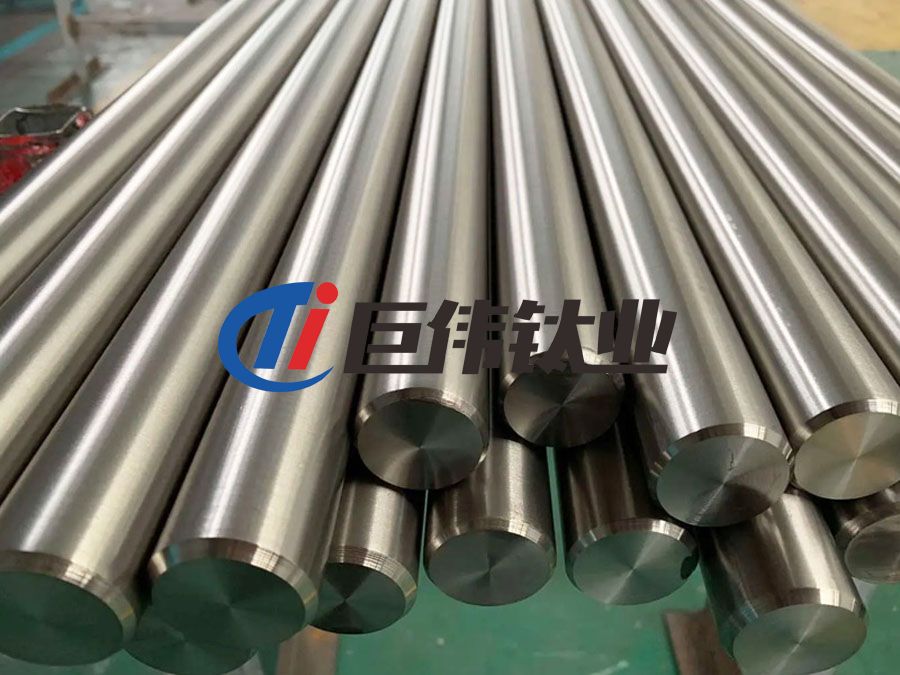
因此,探尋一種加工性能穩(wěn)定,提高材料利用的工藝時(shí)當(dāng)前亟待解決的問題之一[2]。模鍛工藝是一種新的鈦合金棒材加工技術(shù)手段,能夠有效的降低加工成本,提高了材料的
利用率。
1、棒材熱模局部加載成形技術(shù)
1.1 局部加載成形技術(shù)概況
棒材類鍛件為棒材和加強(qiáng)筋組成的復(fù)雜圓形鍛件,腹板和加強(qiáng)筋對鍛件的成形增加了難度。因此,在鍛件成形設(shè)計(jì)過程中必須考慮模壓力對鍛件的影響作用。為了有效的防止熱模鍛造成形過程中整體加載導(dǎo)致金屬沿著徑向大量流動進(jìn)而出現(xiàn)渦流、折迭、紊亂等現(xiàn)象,本次采用局部加載墊板和環(huán)形墊板[3]。在熱模鍛造成形試驗(yàn)過程中,將試驗(yàn)坯料分別放置在環(huán)形墊板中間,坯料和上模之間放置局部加載墊板,可以有效的確保的金屬流動變形充分充填至模具型腔內(nèi),有效的避免了沿徑向流動產(chǎn)生渦流、紊亂等問題。
棒材類熱模鍛造成形加工技術(shù)通常采用整體加載方式進(jìn)行,整體加載技術(shù)在成形過程中當(dāng)加強(qiáng)筋充填至一定程度時(shí),筋部的充填阻力明顯增大,導(dǎo)致大量的金屬沿著棒材中心向四周流動,或者沿著徑向流動進(jìn)而引起紊亂、折迭、渦流等現(xiàn)象,最終使得鍛件充填不到位,使得鍛件質(zhì)量不達(dá)標(biāo)。
若在充填過程中將整體加載方式改為局部加載逐步成形的方式,則可以有效的控制金屬流動的方向,使得金屬充分的充填至加強(qiáng)筋底部,最大程度避免了金屬沿著徑向方向流動
的問題,可較好地避免上述問題的出現(xiàn)概率。
1.2 局部加載成形技術(shù)主要步驟
在熱模鍛造成形過程中根據(jù)棒材鍛件特征,將其分解為兩個(gè)主要步驟進(jìn)行試驗(yàn)。第一步是棒材工件的預(yù)成形階段,該過程就是在局部加載墊板評先壓力的影響下將坯料產(chǎn)生軸向變形,并將其優(yōu)先充填下模筋部等位置,并將金屬沿著徑向運(yùn)移流動直至充分充填環(huán)形墊板位置;由于在充填過程中模具與坯料之間的相對接觸面積較小,加之金屬流動變形速度極快,因此在局部加載過程中坯料的熱損失較小,就可獲得工件預(yù)成形的零件。再完成第一步的基礎(chǔ)上,將預(yù)成形零件最終成形,也就是將棒材鍛件中的環(huán)形墊板和局部加載墊板取出,將預(yù)成形零件升溫至950℃條件下,并將其置于下模腔內(nèi)進(jìn)行最終成形處理。在后期變形成形處理過程中坯料的厚度逐漸減薄,因此與模具的接觸面積逐漸增加。此外,由于最終成形過程中溫度降低速度過快,變形載荷明顯增加。
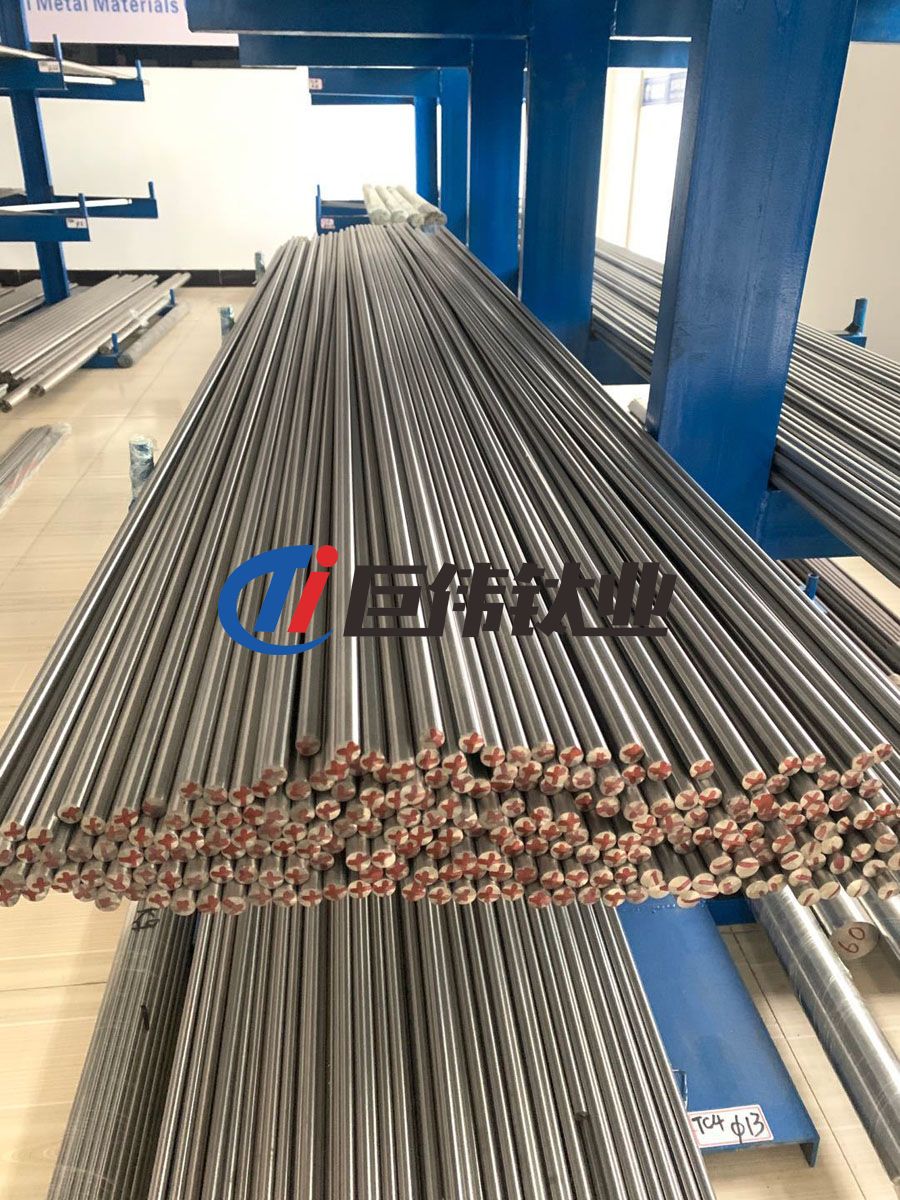
1.3 棒材熱模鍛造成形后顯微組織特征
直至棒材熱模鍛造成形的兩個(gè)重要步驟完成后,對熱模鍛造成形后的鍛件進(jìn)行退火處理,并對鍛件進(jìn)行了顯微組織觀察,在鍛件中可見少量初生α 相組織,呈等軸狀和條帶狀的雙態(tài)組織分布。由于退火溫度接近鈦合金棒材的相變點(diǎn),因此在鈦合金顯微組織中初生α 相含量相對較少。對鍛件進(jìn)行缺陷分析,最終在鍛件內(nèi)未發(fā)現(xiàn)明顯的變形缺陷,說明使用該方法鍛造獲得的棒材質(zhì)量可靠[3]。
使用局部加載熱模鍛造成形技術(shù),與傳統(tǒng)的鍛造工藝相比較,使用該技術(shù)方法使得原材料的利用率明顯提高,極大地降低了材料浪費(fèi)率,間接的降低了鍛造成本。綜上所述,局部加載方式以及熱模鍛造成形技術(shù)能夠獲得質(zhì)量可靠的鈦合金產(chǎn)品其力學(xué)性能遠(yuǎn)遠(yuǎn)優(yōu)于設(shè)計(jì)要求,能夠滿足企業(yè)對鈦合金棒材質(zhì)量的基本要求。
2、常見其他傳統(tǒng)棒材熱模鍛造工藝簡介
常見的棒材熱模鍛造成形技術(shù)除局部加載成形技術(shù)外,常見的鍛造工藝包括:① α + β 鍛造技術(shù),該技術(shù)是在中等應(yīng)變速率條件下將α 合金或者α + β 合金在β 轉(zhuǎn)變溫度下進(jìn)行鍛造的工藝技術(shù),該技術(shù)具有成本低、操作簡單的優(yōu)勢,應(yīng)用較為廣泛;該技術(shù)在鍛造過程中容易出現(xiàn)局部過熱,容易造成鍛件表面產(chǎn)生裂紋,但隨著該技術(shù)鍛造工藝的改進(jìn),逐漸成功的鍛造出了鍛件精度高、表面光潔的成品;② β 鍛造技術(shù),該技術(shù)是在β 相的高溫條件下對鈦合金完成鍛造過程,具有鍛件精度高、變形抗力小的優(yōu)勢,顯著的提高了鍛件的壽命;鈦合金顯微組織中的α 相晶界面明顯增大,多呈網(wǎng)籃組織,提高了鈦合金的抗蠕變性能和強(qiáng)度;③亞β 鍛造技術(shù),是將鍛件在β 相區(qū)加熱處理而鍛造成形過程卻在兩相區(qū)內(nèi)完成的鍛造工藝,該技術(shù)具有與β 鍛造相似的特征,在鍛造過程中主要是將邊界α 相先破碎,使得邊界區(qū)域的α 相逐漸向α 等軸化轉(zhuǎn)變,進(jìn)而提高了鈦合金整體性能。
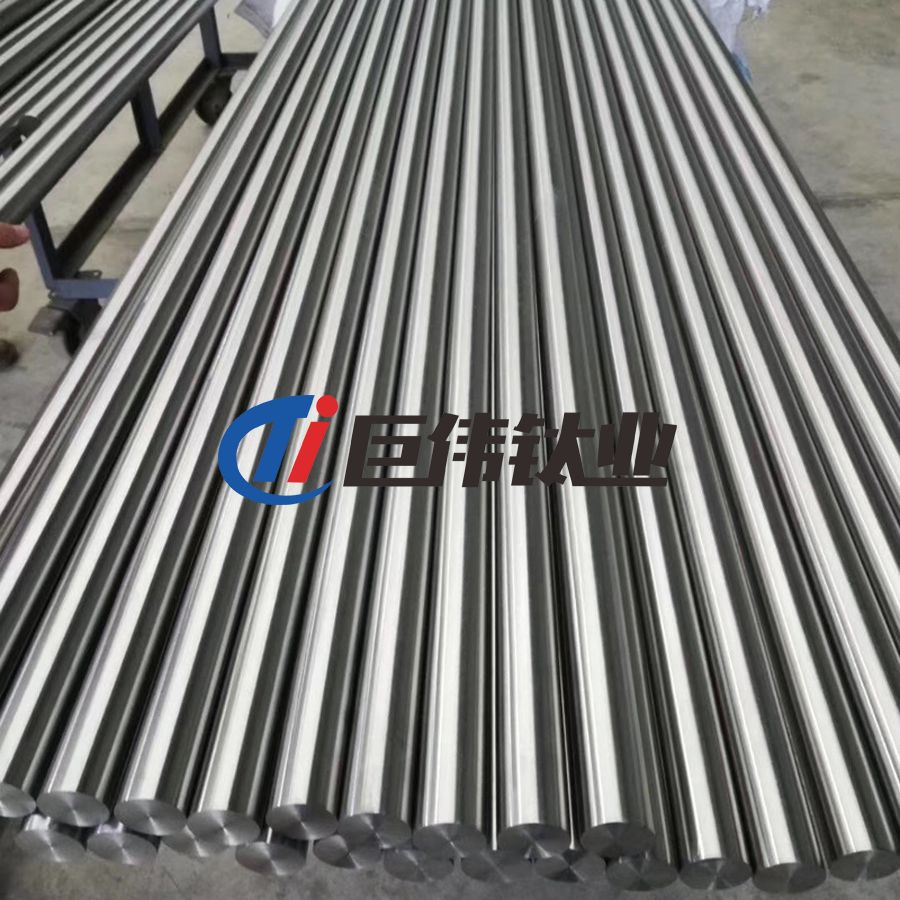
3、結(jié)語
綜上所述,鈦合金棒材因具有優(yōu)越的性能在現(xiàn)代化各領(lǐng)域中具有廣闊的應(yīng)用前景,加強(qiáng)鈦合金鍛造成形工藝的研究工作有助于推動鈦合金材料向更多的領(lǐng)域發(fā)展。文章以鈦合金棒材的熱模鍛造成形技術(shù)為著手點(diǎn),從2 個(gè)方面分析了局部加載熱模鍛造成形技術(shù)的優(yōu)勢,并對鍛件進(jìn)行了力學(xué)性能和顯微組織分析,認(rèn)為本文所選用的加載方式以及熱模鍛造成形技術(shù)能夠獲得質(zhì)量可靠的鈦合金產(chǎn)品,其力學(xué)性能遠(yuǎn)遠(yuǎn)優(yōu)于設(shè)計(jì)要求,能夠滿足企業(yè)對鈦合金棒材質(zhì)量的基本要求。
參考文獻(xiàn):
[1] 李梁, 劉希林. 鈦合金膜板類鍛件熱模鍛造成形技術(shù)研究[J]. 鍛壓技術(shù),2010,35(06):11-13.
[2] 高峻, 李淼泉. 精密鍛造技術(shù)的研究進(jìn)展與發(fā)展趨勢[J]. 精密成形工程,2015,7(06):37-43+80.
[3] 吳瑞恒. GH4169 合金熱模鍛件成形過程的計(jì)算機(jī)模擬[C]. 中國體視學(xué)學(xué)會,2005:59.
相關(guān)鏈接